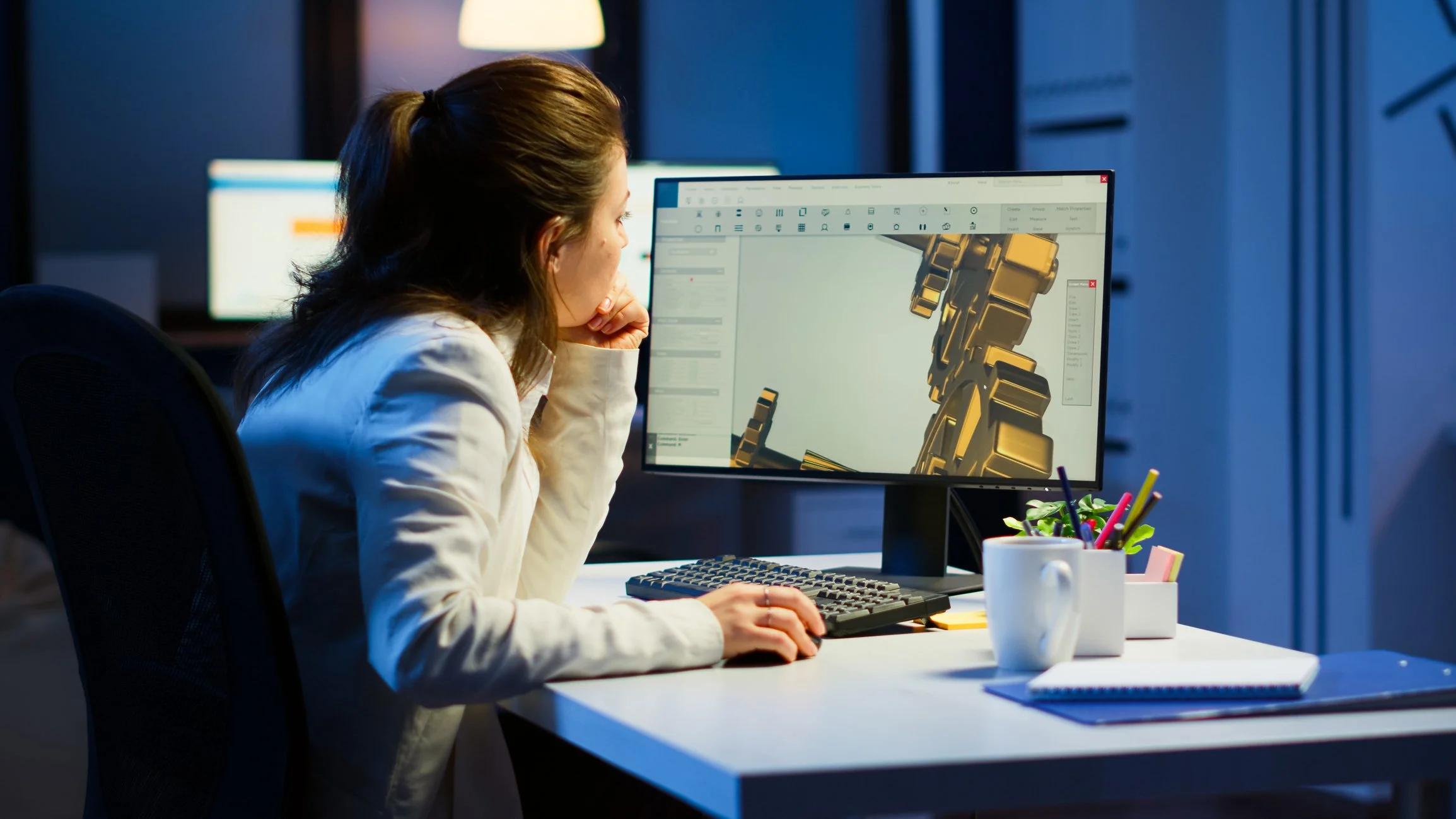
Engineering Services
Harness Our Experienced Engineers for Optimal Product Outcomes
Blue Ridge Industries’ engineering capabilities are the core of the company and culture. Finding quality solutions often originates in excellent design. Our engineering team focuses attention on end-user product requirements and Design for Manufacturing (DFM), to ensure the product performs with high quality as expected in the field and is manufactured as efficiently as possible. This process involves end-to-end project management, Gantt charts, robust requirements determination, CAD design and DFM, mold-flow simulations, prototyping, and project launch support.
Key Capabilities
Full Product Design: CAD-file generation, review and optimization. Identify design features to improve, manufacturability, functionality, or reduce cost. Robust tooling design reviews.
Mold Flow Analysis: Predict fill patterns, cooling behavior, and potential stress points. Optimize gate locations to minimize defects and cycle times.
Product & Part Testing: Validate prototypes or first-run samples against performance benchmarks. Provide data for iterative refinements and final sign-off.
Cost Reduction Strategies: Streamline part designs to use less material. Integrate lean manufacturing workflows for faster, more affordable production.

Our Approach to Engineering
Design for Manufacturability
We closely evaluate draft angles, wall thickness, gating design and placement strategies, and other critical elements to prevent defects and reduce cycle times. By collaborating early in the design stage, we eliminate costly revisions and accelerate your path to market.
Data-Driven Insights
Leveraging simulation tools and production metrics, our engineers fine-tune part geometry, material choices, and process parameters. This quantitative approach ensures each recommendation is backed by real-world data—yielding better-quality parts at lower costs.
Material Selection & Guidance
Whether you need food-grade resins, post-consumer content, durable plastics, or materials for extreme conditions, our team helps you select the optimal resin for strength, durability, and regulatory compliance. We also factor in downstream finishing and assembly needs.
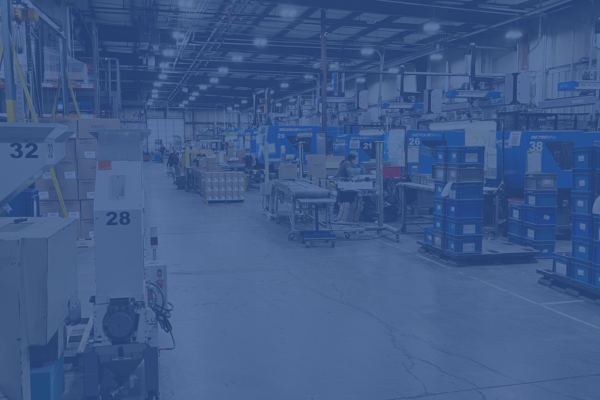
Real-world Applications
Tooling FAQs
-
Yes, we have long-standing relationships with multiple suppliers in North America and Asia and source molds from them.
-
We support prototype, bridge, and production tooling. We regularly run molds with up to 64 cavities, and 72 temperature control zones. We source molds made from aluminum, P20, H13 and other metal based on your requirements and budget.
-
Yes, for tooling where the product has completed our ISO9001 design certified process and where the tooling is sourced directly through BRI, we offer tooling warranties. Please inquire for specifics.
-
Yes, we maintain a robust tooling transfer program that works to bring your existing tooling to production quickly and to make any required changes.
-
Yes, we safely store customers’ molds and maintain records of maintenance activities performed in our ERP system.
-
Yes, we utilize our ERP system to automatically track tool cycles and schedule preventative maintenance on your tooling. This allows us to plan for your production needs and maintain your tooling in the best condition possible.
-
We operate two overhead bridge cranes, a Die-Sep large capacity mold separator/tipper, a large ultrasonic tank cleaning system, mills, lathes, surface grinders, hand tools, and an ULTRAMAX DF Power ultrasonic polisher to maintain our customers’ most critical assets — their tooling.
-
We perform some mold maintenance in the Blue Ridge mold shop. We troubleshoot hot runner systems, replace tooling components, and perform light polishing and machining. If there is significant work required, such as on cores/cavities that affect the part, we work with our vetted supplier partners to complete those repairs quickly and with high quality.
-
To provide the most accurate quote, we need:
3D CAD models of the product(s)
Optional, but requested to avoid any surprise tooling cost increases: 2D drawing with any critical to quality dimensions or special characteristics noted.
Estimated annual volume (EAU): to determine optimal cavitation
Target tool life in years: How many years you expect to produce the product(s).
Target resin type: tools are built for specific resins due to plastic shrink and accounting for any abrasive fillers.
Part finish requirements (core and cavity if different): higher polishes increase cost.
Any country-of-origin limitations: Specify if you approve sending RFQ to Asia tool builders

2D Drawing Best Practices
2D drawings (DWG) are a critical tool to communicate design intent. They describe features or elements important to the represented 3D object. Gain access to our best practices to optimize your 2D drawing for injection molding.

Our Other Capabilities

Ready to Optimize Your Next Project?
Our quality engineering solutions help ensure defect-free parts, faster production cycles, and cost-effective results. Contact us or visit our request a quote page to learn how our team can refine your designs and set you on the path to manufacturing success.